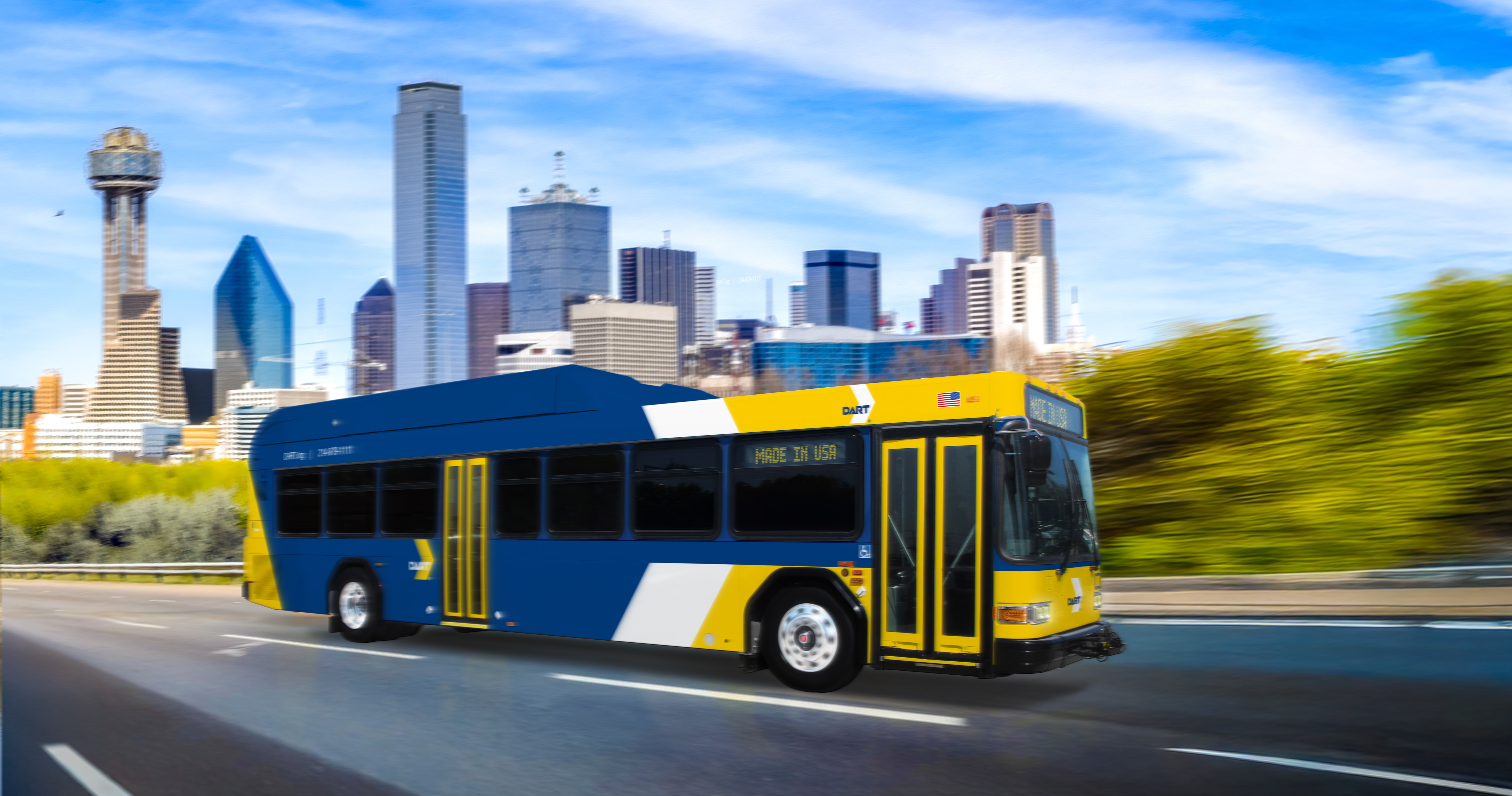
The Buy America-compliant bus manufacturer recently landed a contract with Dallas Area Rapid Transit for 476 buses.
Since its founding in 1890 as a carriage manufacturer, California-based GILLIG has continuously evolved, adapting to the changing landscape of transportation. Today, it stands as the largest transit bus manufacturer in the United States, a testament to its legacy of innovation, quality, and American craftsmanship.
Adding to the company’s steady growth is a recent contract with the Dallas Area Rapid Transit (DART) to build 476 buses for the Big D. The $373.5 million purchase is partially funded by $103 million in federal grants. Delivery of the compressed natural gas (CNG), low floor buses will begin in the spring of 2026.
“This is one of our biggest orders to date,” said GILLIG President and CEO Derek Maunus. “In terms of U.S. sales, we are neck and neck with New Flyer, which is headquartered in Canada, and also sells to Canadian agencies. We are 100% American-built, and our focus is solely on serving U.S. transit agencies.
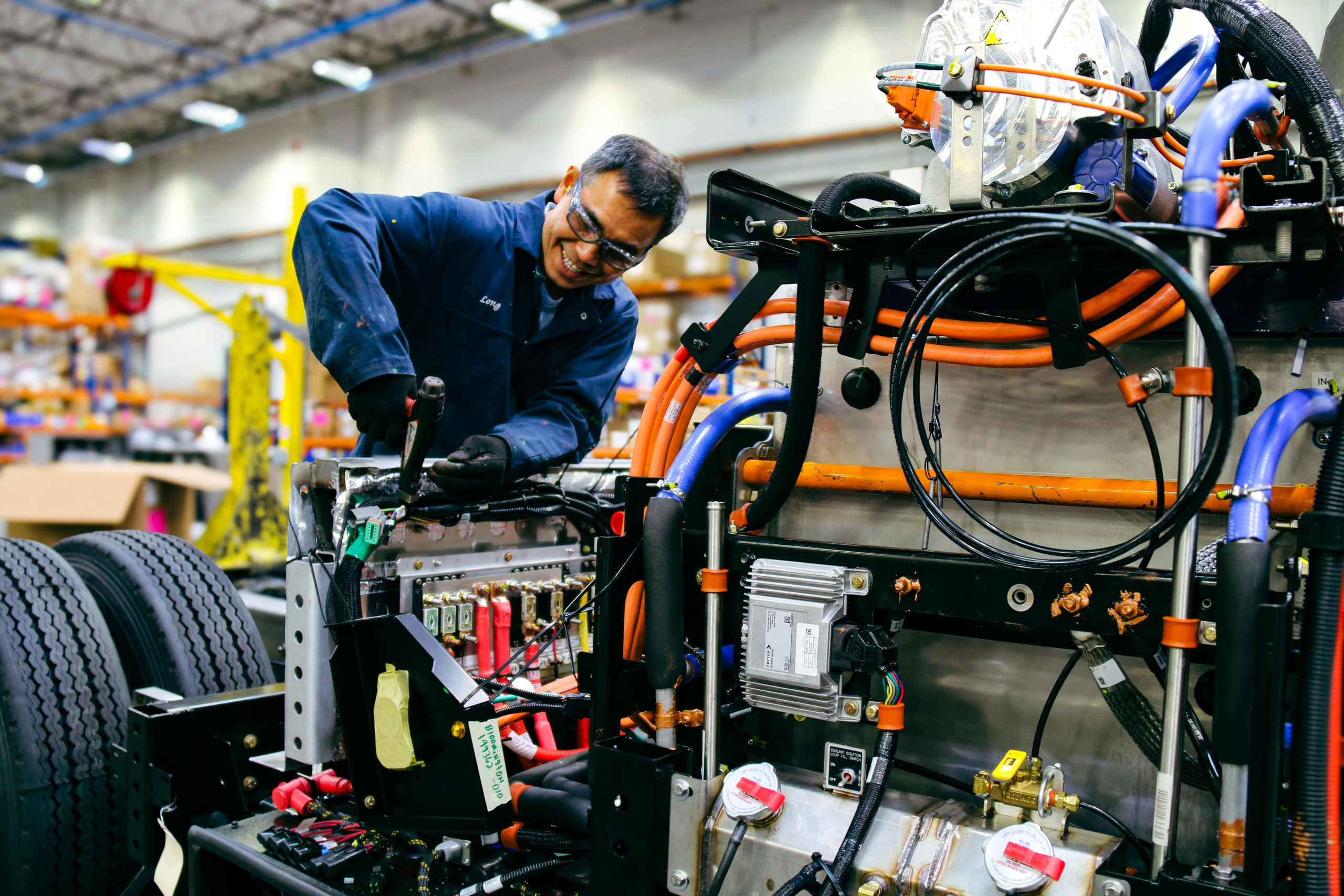
“We have 27,000 buses in operation across all 50 states and are proud of the American jobs we provide. They’re well-paying American jobs with excellent benefits.”
GILLIG has more than 650 people working in its manufacturing facility and overall, the company has about 1,100 employees, all working in the U.S.
After 80 years of production in Hayward, Calif., GILLIG built a 640,000 square foot headquarters facility in nearby Livermore in 2017 that houses its manufacturing plant, engineers, and various offices. The newer facility was built with the idea that staying close to home would help its workforce.
“We moved just 20 miles from our previous location and stayed in California when most manufacturing businesses are leaving California because this is essential to our employees,” said Maunus. “These are the people that have helped make GILLIG successful over the years. We are not going to reward that success by moving jobs away.”
GILLIG has maintained a strong, decades-long partnership with its unions, fostering stability and quality jobs for its workforce. Since 1976, Teamsters Local 853 has represented a significant portion of GILLIG employees, while Auto, Marine & Specialty Painters Local 1176 has been a valued partner since 1968. Reflecting this strong relationship, GILLIG’s union employees recently approved a new five-year contract with an overwhelming majority on the first ballot, reinforcing their confidence in the company’s commitment to competitive wages, excellent benefits, and long-term stability.
““GILLIG sells to 70 percent of the transit authorities across the United States with a 40 percent market share. We are making it happen in the U.S., and I think we can be the poster child of how federal dollars should be spent for American jobs and well-paying American jobs.”
GILLIG President and CEO Derek Maunus
While originally a carriage repair shop, GILLIG adapted with the rise of the automobile, shifting to truck and military vehicle manufacturing. Later known for producing school buses, the company transitioned to the transit bus industry in the late 1970s to meet the growing demand for durable, American-made public transportation solutions.”
“We are a very focused organization proudly working on transit buses only,” said Maunus. “We’re proudly American-owned, we’re a family business, and we’re only focused on the U.S. transit market.
“Our industry, because of the federal funding tied to our customers, it needs to meet the Buy America requirements, and we always have. From GILLIG’s perspective, we’ve invested a lot in the zero-emission product, and it’s definitely been a focus of ours, but we are agnostic when it comes to the propulsion.
“We’ve never driven one technology over the other, but we’ve invested in our organization and our R&D is based where we believe the market is going. For a while it was zero emission. We sell CNG, hybrid, battery electric and we are going to support what the customer wants and what the customer needs.”
All GILLIG’s customers that use federal funds must purchase from a company that meets the Buy America requirements. If you are going to leverage federal dollars to invest in infrastructure, those funds need to be supporting American jobs.
“To put it in perspective, GILLIG reinvests over a billion dollars each year into 875 U.S. suppliers,” said Maunus. “Every bus we build is made up of parts sourced from across the country, with suppliers in more than 40 states. When a transit agency purchases from GILLIG, that investment flows through our entire supply chain, supporting American jobs and businesses nationwide.
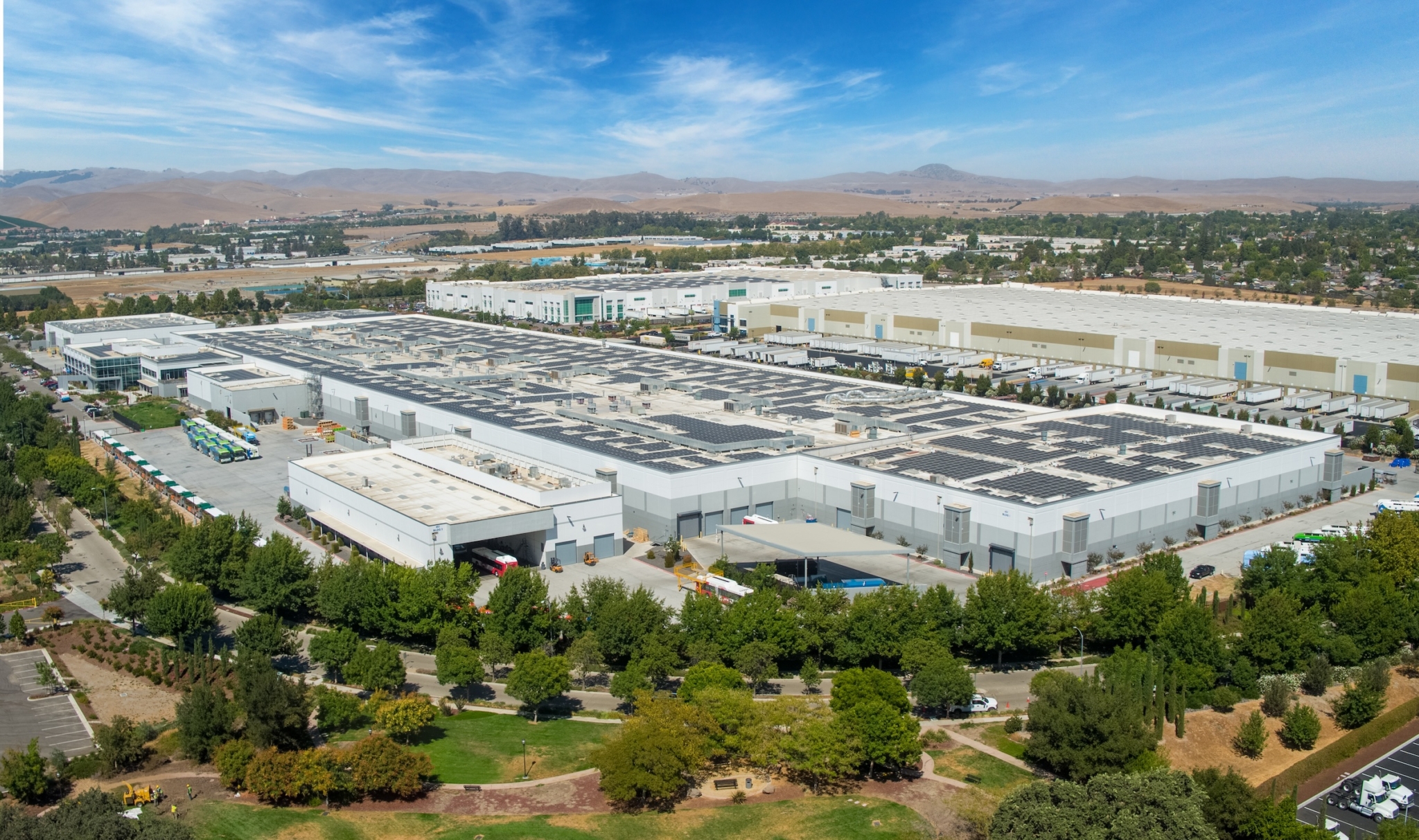
Beyond its impact on suppliers across the country, GILLIG’s investment in American manufacturing also strengthens the local economy by supporting stable, well-paying jobs. That commitment to its workforce has resulted in industry-leading employee retention and a highly skilled team dedicated to building the best buses on the road.
“We are lucky to have such an experienced workforce. Our turnover rate when you don’t include retirement is under 2% in manufacturing. That is unheard of in the manufacturing business.
“We have something that is very special here and that is our workforce. They are very well compensated and for the skill set they are the highest in the area, which tells me that they are probably close to the highest in the country. We take care of our employees, and our employees take care of us.”
GILLIG does not sell to some of the largest cities, like New York and Los Angeles, but services many of America’s larger municipalities, having delivered buses to Pittsburgh, Seattle, San Antonio, Austin, Minneapolis and more.“ GILLIG sells to 70 percent of the transit authorities across the United States with a 40 percent market share,” added Maunus. “We are making it happen in the U.S., and I think we can be the poster child of how federal dollars should be invested to support American manufacturing and well-paying American jobs. Our story is proof that American manufacturing can thrive when companies thoughtfully and strategically invest in their workforce, their communities, and the future of their industry.”