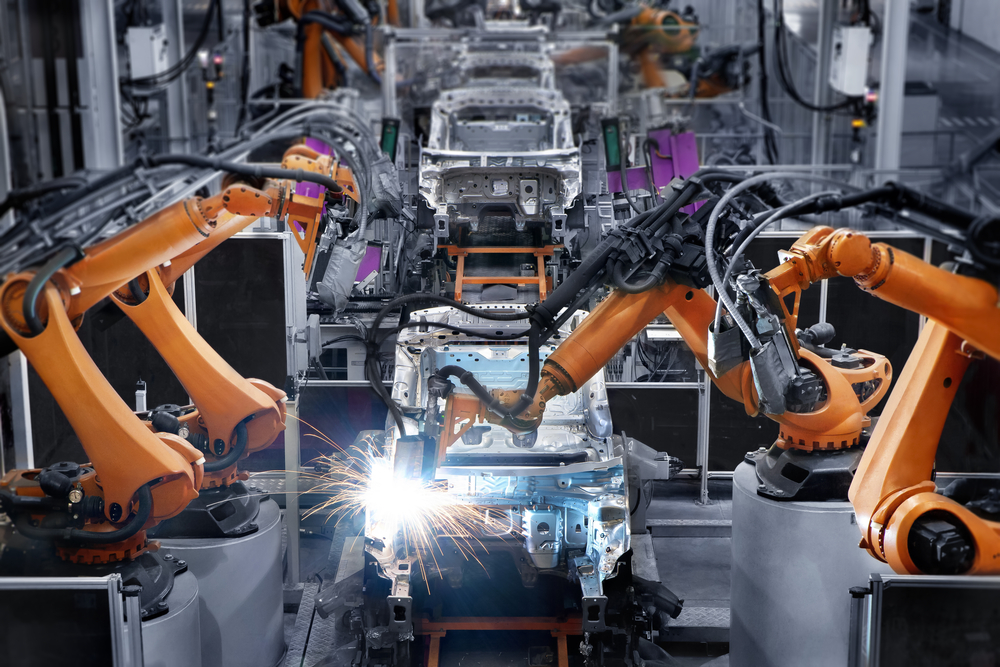
Some fear automation, but already it has created new roles for humans to fill.
Editor’s note: The following piece is a submission by Casey Heigl, marketing manager for Heigl Technologies, a Minnesota-based manufacturer of adhesives, sealants, and industrial chemical solutions.
American assembly lines have seen significant changes since Henry Ford first used them to innovate the automobile manufacturing in the early 20th century. Today’s assembly lines are fast-paced work environments operating on tight schedules to meet ever-increasing volume goals.
Meanwhile, increased automation has nearly eliminated the need for low-skill labor in favor of highly skilled workers who monitor, maintain, and improve on existing automation solutions.
As the nature of labor evolves with the development of more sophisticated technologies, the manufacturing industry needs to adapt to keep American workers engaged and promote growth.
To understand the direction American mass production is headed toward, the history of assembly lines offers a few lessons.
A Window into the Future
Henry Ford started the mass adoption of the assembly line process in American manufacturing in the early 1900s. At this time in history, a large gap existed between the wealthy and the working classes. The working class produced the goods; the wealthy class consumed them.
Labor was specialized, which meant producing a product was time-consuming and expensive. Henry Ford took the assembly line and transformed it, allowing goods to be made at a much quicker speed and significantly lower costs. Ford also implemented an 8-hour work day (something America’s labor unions had fought for decades to achieve) and paid each assembly line employee $5 per day.
The increase in wages changed the demographic between the wealthy and the working class. Instead of merely producing the goods, the working class could afford to purchase some of those goods. In turn, this boosted the demand for more products (and therefore more workers).
The enhanced assembly line and the growing popularity of mass production changed the face of America. It helped United States become a superpower and one of the wealthiest countries in the world.
Assembly Lines Everywhere
Fast-forward to the present day, and the assembly line has become ubiquitous to modern life. It might not be immediately apparent, but assembly lines are everywhere.
They appear in everything from the housing market to department-store clothing. In housing, rows of dwellings pop up in a few months' time. The process has become so streamlined that it takes just a few days to pour foundations, erect frames, and install roofs.
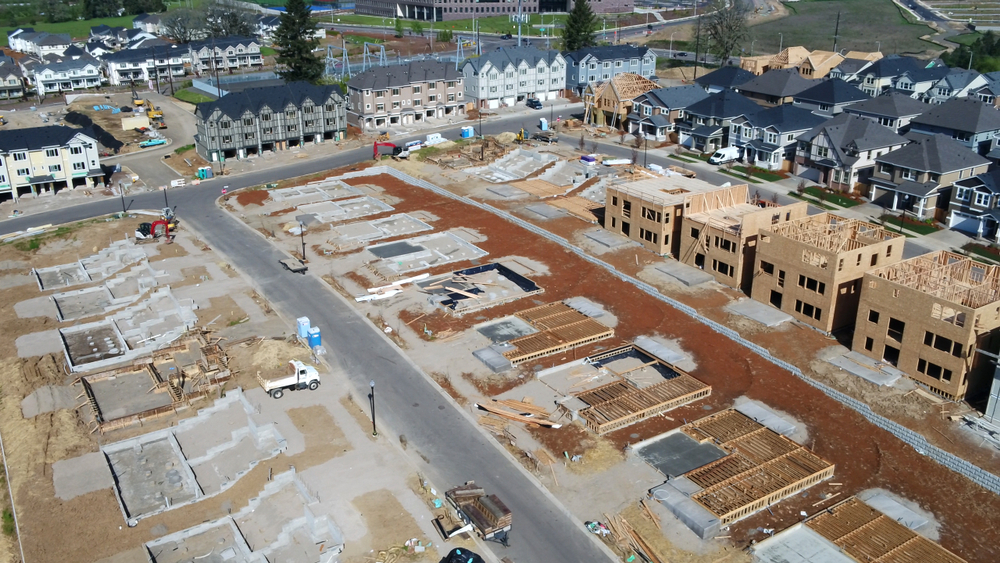
Take a walk through any modern department store, and you find evidence of assembly line work and mass production on every aisle. Furniture with slight variations to account for differing tastes in style or décor inhabit attractive settings. Clothed mannequins model the same shorts or dresses, but in a rainbow of colors. These mass-produced goods are affordable and widely obtainable due to the quick and low-cost processes employed today.
The assembly line has come a long way since Ford's original iteration, and that drive to optimize continues.
Modern mass production takes advantage of new technologies and materials. New developments, such as hot melt adhesives made to bond specifically to their substrates, improve the speed of production by simplifying steps or reducing the time it takes to complete them.
Today, assembly line factories rarely build products from start to finish. Instead, they focus on assembling specific parts in one region that produces workers skilled at a particular craft. These parts then get shipped to another plant for further assembly.
These improvements come as an effect of increasingly more accurate data collection, which now allows company executives to check on manufacturing data in real time. This keeps them abreast of quality control, production timelines, and product quantities, allowing them to start the innovation process anew and iterate on new production methods.
The Realities of the Modern Assembly Line
Despite advancements to manufacturing technologies, methods, and materials, the core concept of assembly lines remains the same today as it was during Ford’s time: create specialized workstations for each part of the assembly process.
This focus enables workers to perfect the technique for their station. Workers can then quickly and expertly complete a step in the process without requiring in-depth knowledge of how that step affects other steps down the line or the final product.
Products move from station-to-station, receiving parts or undergoing changes at each location. Eventually, the product reaches the end station, where its assembly is complete.
Automation has created new roles for humans to fill. In some of the most advanced assembly lines in America today, humans play the part of teacher and supervisor. They “train” the robots to do the jobs they once filled and monitor automated processes for continued accuracy.
Unlike Ford’s assembly line, however, lines in America today increasingly extract the human element from the equation. Doing so removes the need for workers to perfect a specific technique, replacing humans instead with automated processes and robots that only need training once to achieve mastery.
With the accelerating pace of research and development on automation and robotics, experts predict a future where entire American assembly lines require only a few human workers.
Understandably, this has caused assembly line workers to fear for their future. But the past also shows that change should not be feared.
When Ford instituted his assembly line process, he alienated many skilled workers of the time, who saw their roles diminished. He also eliminated the lowest-skilled roles, which served merely to aid the skilled craftsmen, and replaced them with hooks and conveyor belts.
The simplification of skilled work, however, created opportunities for unskilled individuals to train more rapidly into the newly created assembly line roles. Similarly, the automation of today’s assembly lines necessitates decisive adaptation to changes as they emerge from beyond the horizon.
Rising to the Challenge
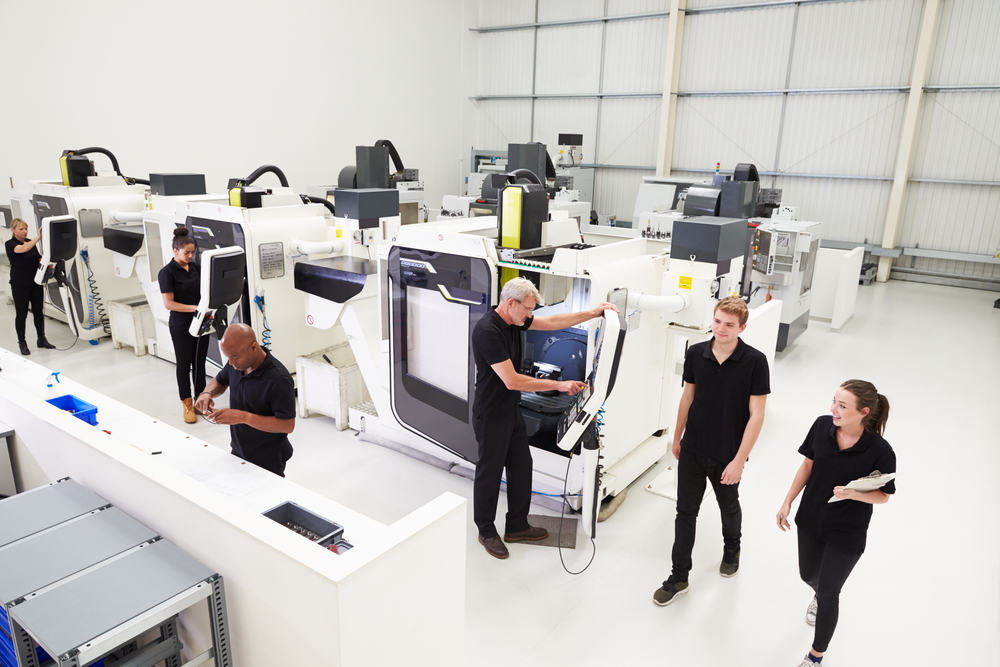
Automation, like Ford’s assembly line, eliminates the lowest-skilled roles and reduces the skill level required to perform previously more experience-demanding tasks. Already, robots take on complex jobs, such as welding, testing, and painting – domains that were once exclusive to highly trained humans. In the wake of job eliminations, however, automation has created new roles for humans to fill.
In some of the most advanced assembly lines in America today, humans play the part of teacher and supervisor. They “train” the robots to do the jobs they once filled and monitor automated processes for continued accuracy.
As automated processes improve, so too do their control schemes and feedback systems. This simplification then allows workers who lack the skills to operate automated systems to train more quickly into the new maintenance and monitoring roles.
As grim as some might think it to be, the future is bright for American industry because of automation.
Assembly lines have historically mirrored the progress of society and the economy in the United States. If the fear mongers of Ford’s time were to be believed, we shouldn’t have as much to be proud of as a nation today.
And modern assembly lines are less grueling than they were a hundred years ago. Workers are paid advantageous wages, and their work conditions have improved.
After all, when Ford instituted the 8-hour work day and paid assembly line employees $5 per day, he did so under his own initiative. His reasons for doing so may not have been purely benevolent – Ford wasn’t exactly a liberal champion of the working class, after all — but the effects of his actions remain evident today.