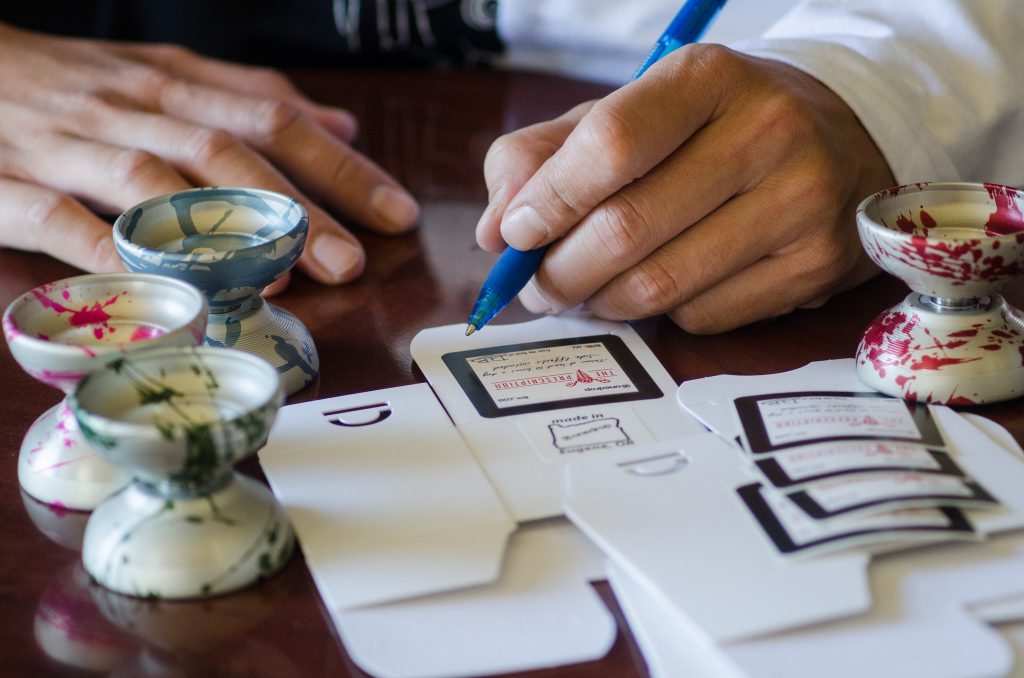
No longer just a toy, yo-yos are a serious sport — and a serious business.
Do you remember the last time you “walked the dog” or “rocked the baby?” Or maybe at one time you “hopped the fence” or took a trip “around the world.”
Before we trick you into thinking these are activities of your everyday life, let us explain. We are referring to the names of different artistic kinds of tricks. Yo-yo tricks.
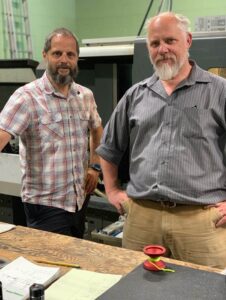
For those who’ve somehow never seen one, a yo-yo is a toy that consists of an axle connected to two disks, with a length of string looped around the axle. It is played by holding the free end of the string allowing gravity or the force of a throw to spin the yo-yo and unwind the string. The string winds itself back again onto the axle and is ready for the next throw.
Simply, this is yo-yoing.
Today is National Yo-Yo Day. Like many toys, nearly all yo-yo manufacturing has been outsourced to countries like China and Mexico.
But 12 years ago, two American yo-yo enthusiasts stepped in to fill the void by launching One Drop, the only mass production-level, Made in America yo-yo manufacturer.
Longtime friends David Metz and Shawn Nelson opened a design business in Eugene, Ore., in 2001, working with a variety of materials to make niche products for their customers. One day, they were approached by a design student from the University of Oregon who was taking part in a school project where his assignment was to seek out mentoring at a local design company.
“He was an avid yo-yoer, so he caught our attention and kind of explained everything that was going on with yo-yos at the time,” said Metz, who at the age of 50 has had his fair share of yo-yo experience. “He said he had an idea for one, and asked if anybody here would make him a yo-yo. So, I said alright, let’s see where this goes.
“So, we worked on a design with him and built one, and we said we are going to try and sell this thing. Well, it was kind of an instant hit and put us on the map and we ran with it from there. It was the first product of our yo-yo line.”
Metz and Nelson operate One Drop Yo-Yo out of a 2,500-square-foot shop in Eugene with one other employee. They produce 200 to 400 yo-yos per batch and do not keep a large inventory because they can quickly fill a large order.
One Drop makes about 8,000 of its own signature products per year, and also manufactures yo-yos for other companies on a limited basis.
The company sells both plastic and aluminum yo-yos. It has created about 60 models since the business began in 2007, but only offers three of four at a time for sale. They sell in the price range of $50 to $100, but they will gladly make you one of their titanium models for $300.
One Drop is also working on a stainless-steel yo-yo.
“The internet has changed the yo-yo business,” Metz said. “Since the early 2000s, you can go online and read this history of all the gear and all the tricks are documented on YouTube. It’s more self-sustaining for that reason.”
In the 1960s, wood and plastic yo-yos were the norm, but today aluminum is the material of choice to produce a high-end yo-yo. While the entertainment purpose of a yo-yo remains the same, yo-yos now have a more advanced, high tech look, and yo-yoing has become a serious sport.
“Plastic is generally low cost, mass market and there are small-time hobbyists or tiny companies that will do hand-made wood yo-yos. That’s about the only kind of wood you are going to find these days,” Metz said. “The majority of high-end, high-performing yo-yos are aluminum. There still is a lot of plastic out there coming from China, but for the high-end, aluminum is the standard for the industry.”
The two halves of a One Drop yo-yos are not flat like the traditional disks. The aluminum is more of a concave shape that is formed on several Haas CNC metal lathe machines.
The two halves are held together by an axle, but modern yo-yos also have a ball bearing on the axle to increase the spin time when the yo-yo is thrown. That allows for extra time to perform the amazing tricks of today where yo-yoers often wrap the string around their arms and bodies.
Co-owner Nelson, a former machinist, had the tech experience to make use of CAD software and convert it into code to produce a process that allows the metal lathe machines to cut the aluminum in varying sizes and shape. The intricate colors and patterns come during the anodizing process done by GruntBull Anodizing in Gettysburg, Ohio.
The packaging is done in Seattle, and each box has a “Made in Eugene” sticker attached.
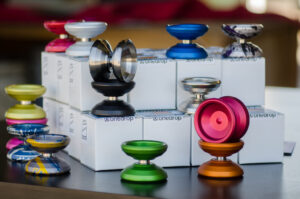
Not only are One Drop Yo-Yos made in the United States, but the company also sources its aluminum from a supplier in Utah that provides American-made Alcoa or Sapa aluminum.
“We are paying a bit more for the aluminum because of the tariffs, but we are pretty hard-headed about it,” Metz said. “It will never be outsourced to China. The point of our business is we make it here. That’s the conception of it, and that’s what we are here to do. If we can’t do that, we are not going to do it. That’s just how we are.
“You kind of got to be crazy to do it as small company, because there is not a lot of incentive, but we will remain American-made. There is not government incentive for us to be doing it this way and we could easily switch to China and the system wouldn’t care.
“But you know, around us is the whole eco-system. We are supporting the company that sources the metal and they are buying from Alcoa. We buy American machinery from Haas and we supply money to them, and we pay for the anodizing to a small company in Ohio helping to support them. Our existence is supporting American companies all around us.”
One Drop yo-yos can be purchased through the company's website or at select specialty stores and yo-yo shops.
Editor's Note: Blogs like this one are intended to highlight companies that support American jobs and that make great products in the United States. We rely on companies we feature to provide accurate information regarding their domestic operations and their products. Each company is individually responsible for labeling and advertising their products according to applicable standards, such as the Federal Trade Commission's "Made in USA" standard or California's "Made in USA" labeling law. We do not review individual products for compliance or claim that company products comply with specific labeling or advertising standards. Our focus is on supporting companies that create American jobs.