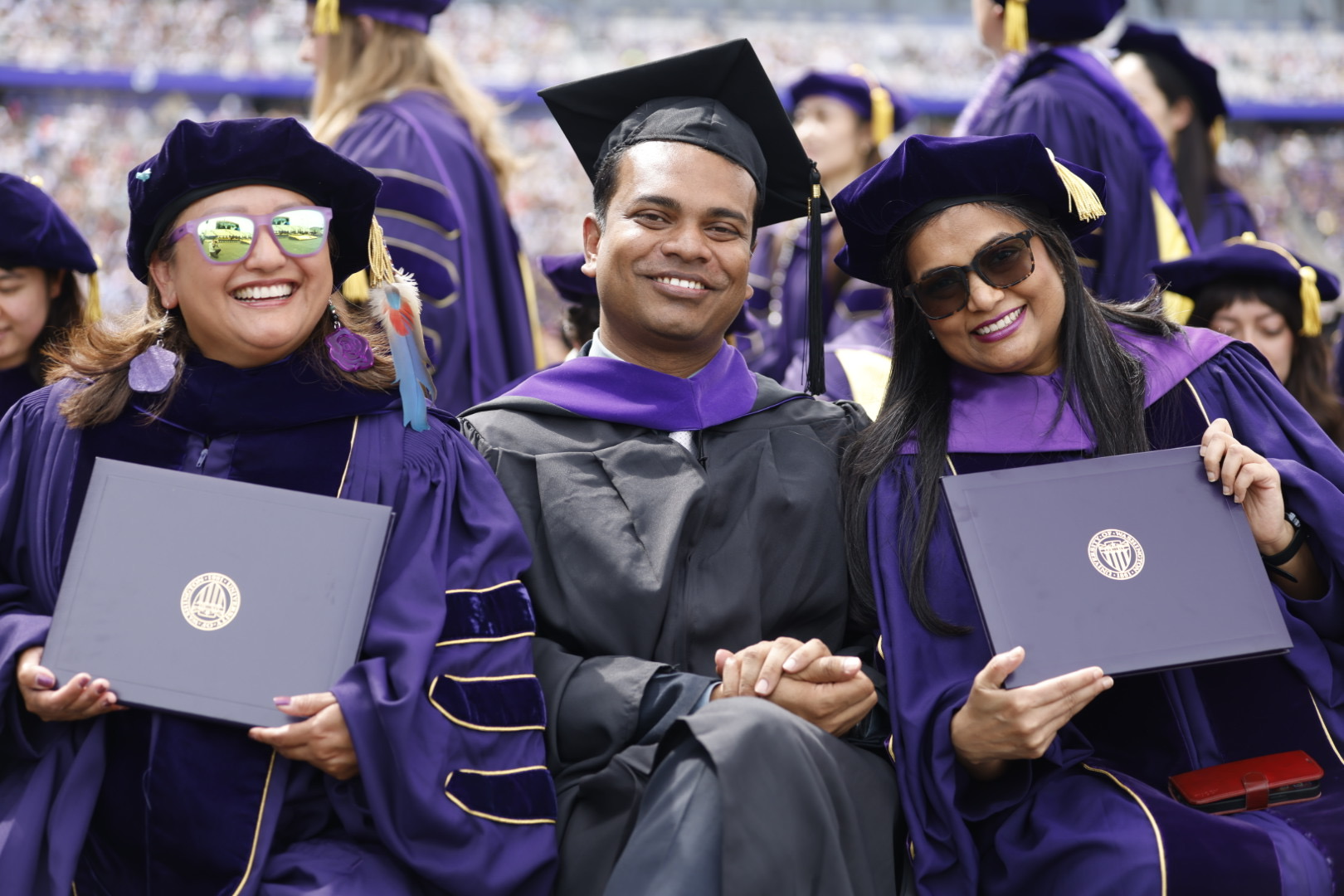
Oak Hall Cap & Gown makes big-day apparel for thousands of college and high schools each year. Here’s how they do it.
Graduating college students have absorbed a great deal of newfound knowledge, studying right up to the pomp and circumstance of their commencement ceremonies.
The final lesson of their college days is found in the caps and gowns they wear to “walk” across a stage and receive their degree. It is Oak Hall Cap & Gown, the outfitter of many thousands of students for their big day, who teaches them about the production quality of an American-made garment. They also learn about sustainability, as Oak Hall’s student gowns are made from 100% recycled plastic bottles.
Oak Hall Cap & Gown is a Salem, Va., manufacturer that has been continually in business since 1889. The company has four sewing locations in Southwest Virginia and one in Plantersville, Miss., as well as a warehouse in Roanoke. In all, Oak Hall occupies more than 450,000 square-feet of manufacturing and office space.
Donna Hodges is Oak Hall’s executive vice-president and has more than 40 years of experience working at the cap and gown concern.
“We are sewing caps and gowns 48 weeks out of the year just to have enough to supply all the colleges and high schools we do throughout the country,” said Hodges. “We are bigger in colleges than we are in high schools. We make over 2 million caps and gowns a year.
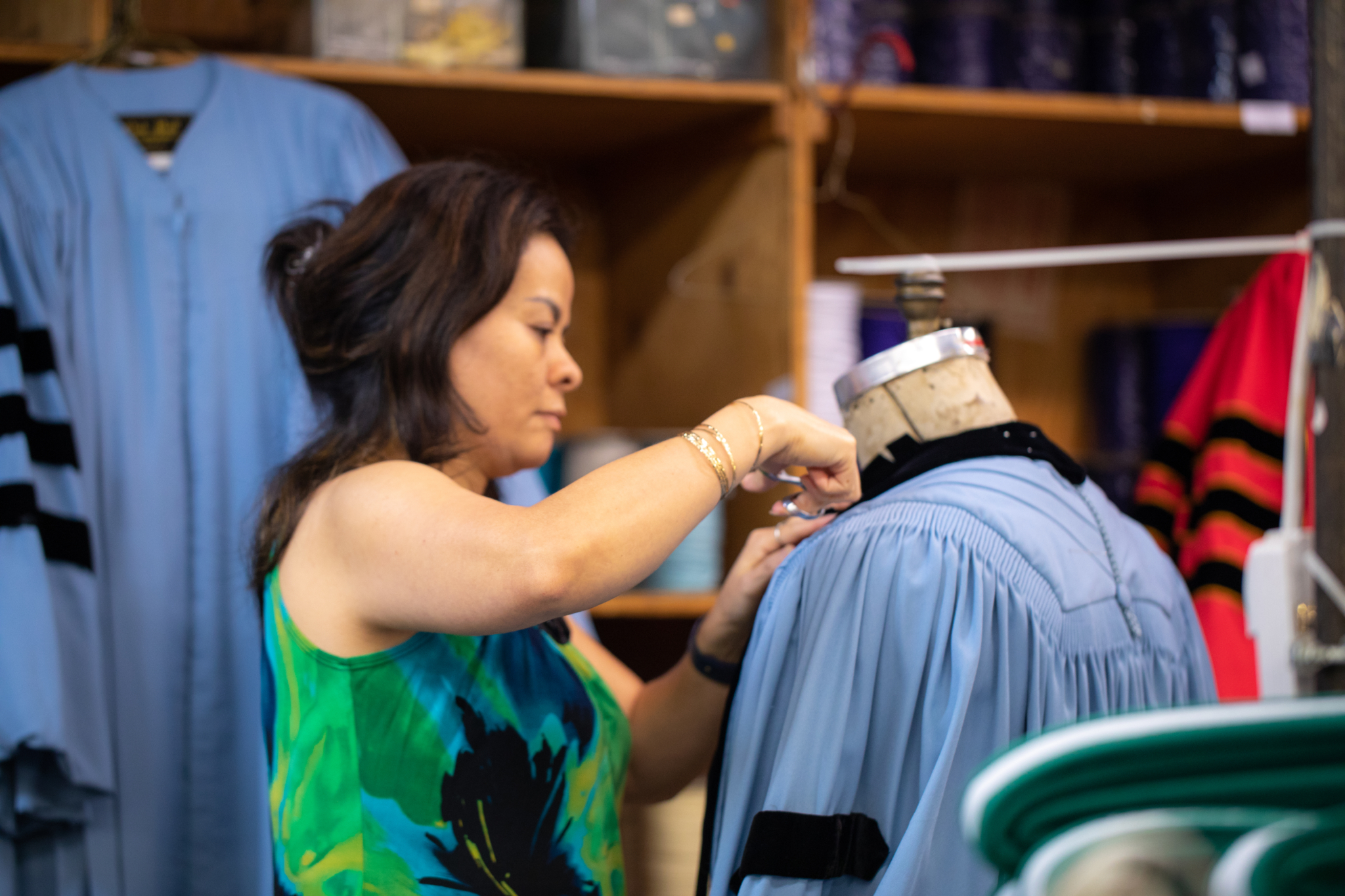
“It’s a fun business. We get people at one of the most exciting times of their lives. Students are so proud of putting on that cap and gown and walking across the stage. It’s one of the happiest occasions.”
Early May and Mother’s Day weekend are the prime times for college graduations. Oak Hall’s 500 employees realize this is crunch time, so the sewing machines are buzzing six days a week with plenty of overtime hours earned. When there are shorter lead times, Oak Hall is up to the task of having caps and gowns ready for an institution’s important day.
“Every single gown is touched by people at sewing machines,” said Hodges. “Obviously, in the last few months with talks of tariffs and all that, it is a good time to be in a business where we are not relying on overseas manufacturing and purchasing. It’s a good time to be an American-made company.
“We do see that a lot of people still care about American-made. There’s always going to be those out there that it’s just all about the lowest price they can get and nothing else matters. But there still are a lot of schools where it means something to be an American-made company.”
Oak Hall began as a family-owned business and remains so today. It was started in 1889 by the Rosenberg family in Roanoke, and three generations of Rosenbergs operated the factory. Many years later it was sold to Alex Grass and the Grass family still owns it today; Grass’ daughter, Elizabeth Grass Weese, serves as the CEO.
The only major change in the caps and gowns over the years is the use of recycled plastic bottles to create the fiber used in manufacturing the regalia. It takes about 25 grounded plastic bottles to make the fabric for one cap and gown.
“The majority of our fabric comes from Milliken in South Carolina. They are one of the largest textile and fashion apparel manufacturers out there and they have looms running all the time weaving Oak Hall piece goods,” said Hodges. “Unifi, which is in North Carolina, processes plastic bottles and turns them into the fiber that goes to Milliken to weave the fiber into the fabric that gets trucked up to us here in Virginia for our manufacturing.”
Oak Hall’s four Virginia factories are in Salem, Wytheville, Chilhowie, and Independence. Not exactly urban manufacturing hubs.
“The reason that they are spread out – they’re actually spread out in a square – is because all of them are 60 to 90 miles away from the next one because in the textile industry with sewing you have to go where there are available sewers,” said Hodges. “They are not going to drive an hour to go to work, so we open these plants in the smaller communities where there’s a really good source of sewers.
“We do have one sewing factory in Mississippi that we added after Covid because we had grown, and even with our four facilities we weren’t getting enough out.”
Oak Hall’s roster of college and universities that are clients is made up of schools throughout the U.S. including major outposts that include the University of Michigan, Michigan State University, University of Washington, University of Texas at Austin, Kentucky, Louisiana State University, Miami, Clemson, South Carolina, North Carolina, American, Vanderbilt, Johns Hopkins, and many more.
“We service about 1,800 colleges including the Ivy League – Penn, Princeton, Brown, and Columbia – and we do anywhere from 2,000 to 3,000 high schools,” said Hodges. “We have done 6,000 to 8,000 for Ohio State, University of Texas is about 8,000, and Columbia walks now close to 10,000.
“Those are the big schools be we also have smaller schools that walk 500. The average is about 2,500. Most of our high schools are two, three hundred tops.”
Prior to the Covid-19 pandemic, most of the ordering was done by universities that would order in bulk.
“If they were graduating 1,000 students that order would be say 1,400 or 1,500 sets in various sizes and we would send them to the campus bookstore. The students would come into the bookstore and pick up and pay for their sets, so we would bill the university or the bookstore,” said Hodges. “When schools were closed for Covid we had to quickly pivot to opening websites for all of these schools.
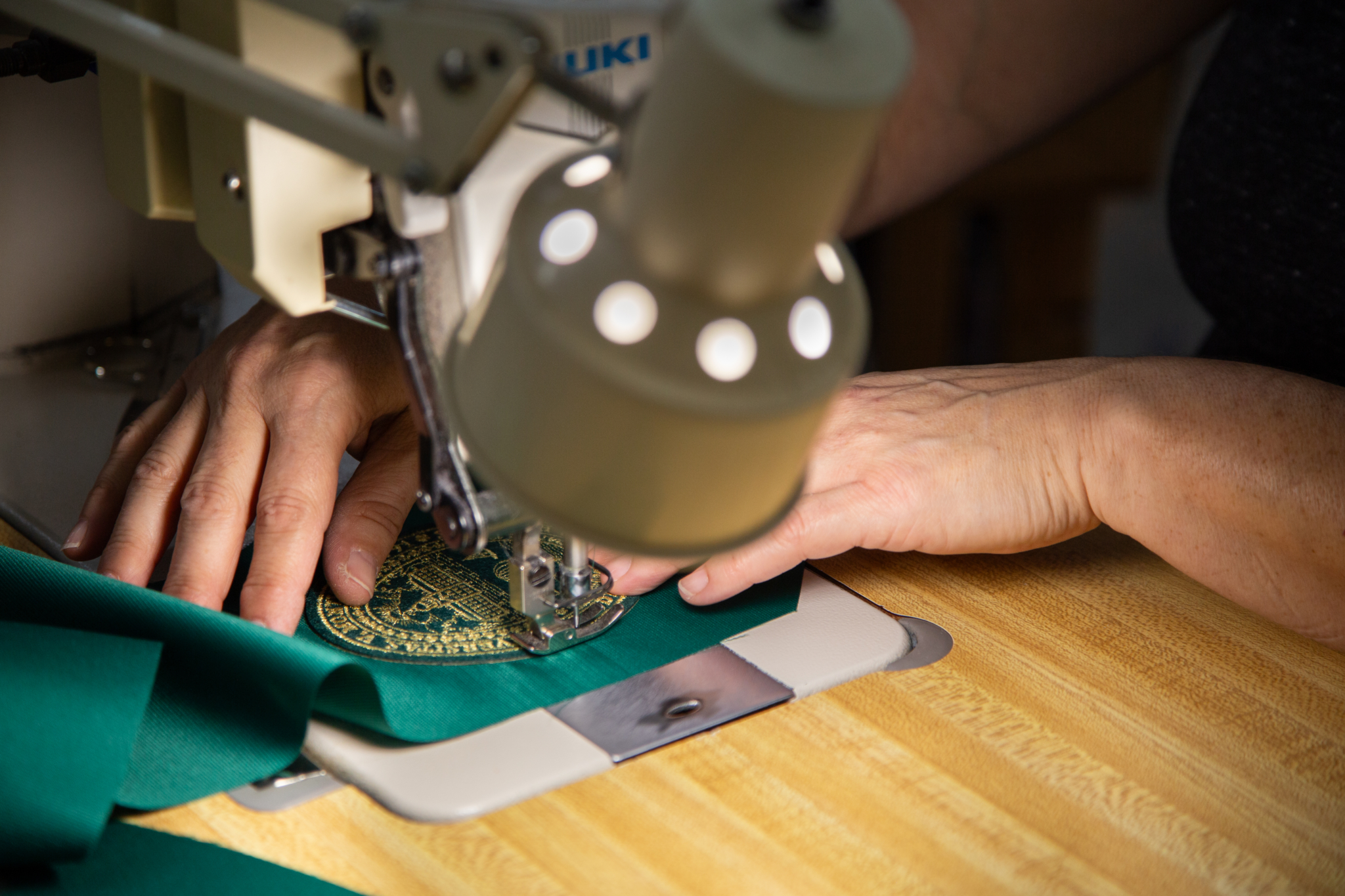
“Today we have over 1,000 micro sites so we have a separate website for every college. The student goes to the website and orders their cap and gown, and it comes directly to us. We manage the website and then we home-ship to each student.
“It was a little bit of a challenge starting out because we need to have a lot more hands on where we have to touch every cap and gown individually, box it up and ship it out the door versus pack a thousand cap and gowns in various sizes and ship them out altogether.”
Another challenge that Oak Hall has mastered is the sizing of the regalia. Most of their gowns are for students who are 4’7” to 6’ 7” tall. But there is always the unexpected.
“Even though we are sewing all year it always happens that there is a university that might be graduating a bunch of basketball players as tall as 7 feet,” said Hodges. “The next year there is a bunch of gymnasts and everybody is 5 feet.
“The employees here are experienced and can quickly pivot when needed to meet deadlines,” added Hodges. “Most of our employees here have a lot of tenure. We have a lot of 40-plus year employees and a lot of 25-year plus sewers.
“The company is really good to the employees, but the employees are really good to the company. We have never laid a person off in the long history of Oak Hall Cap & Gown.”