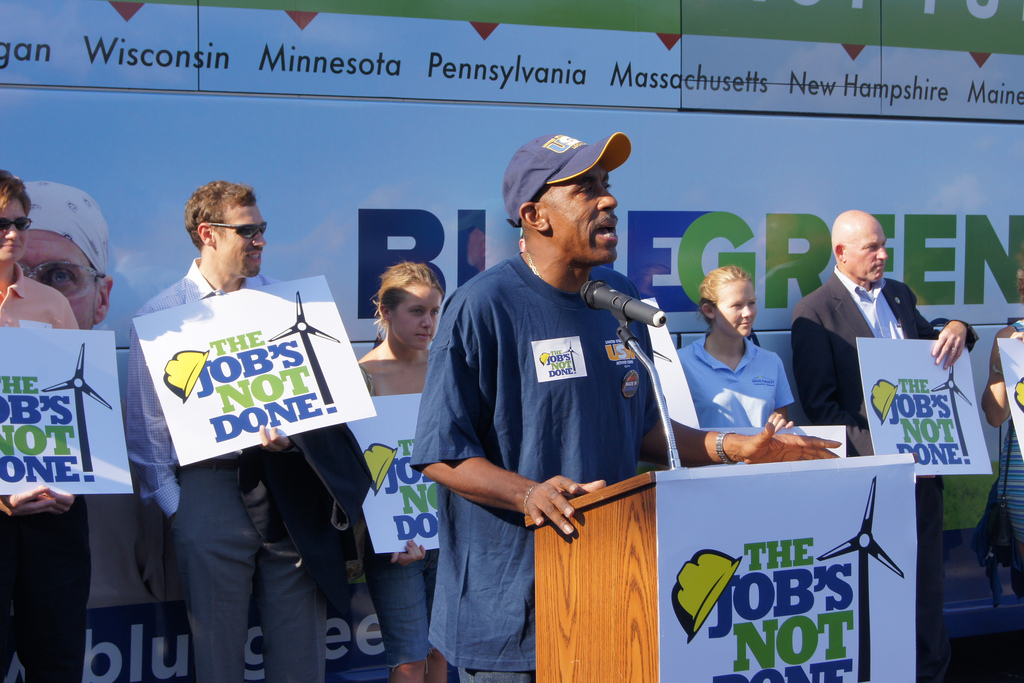
A look at how one baby boomer is coping with losing his steel job of nearly 25 years.
Lindsay Patterson had worked for nearly 25 years at Allied Tube and Conduit Corp. in Northeast Philadelphia when the plant ended operations on Oct. 5, 2015.
Out of a job at the age of 61, Patterson didn’t have many options. He found it difficult to find a similar job, and considered Trade Adjustment Assistance (TAA), a federal program that retrains laid-off manufacturing workers for new careers.
But Patterson quickly realized TAA is not really beneficial to a man of his age.
“They talk about retraining like that is something easy to do. Well here I am, 61-years-old and I’m going to go back to community college to do what? Unless I become a genius and become a doctor, I’m still not going to get any work,” Patterson said. “Not any real work. They keep saying retrain, but at this age, for what? That’s okay for young kids but for older folks retraining is too late.”
Allied Tube closed in 2015 after its parent company, Atkore International Inc., decided to stop making sprinkler and fence pipe. The remaining work at the plant was shifted to Atkore facilities in Phoenix and the Chicago suburbs.
"I thought I would retire from there, but the rug was pulled out from under me…" Lindsay Patterson
Unfair trade was to blame. Countries like China manufacture the types of steel products that were made by Allied Tube, but they also heavily subsidize steel makers and do not require them to follow labor or environmental rules.
At the same time, China is producing way too much steel, and it needs to do something with its excess capacity. So, it dumps it into the U.S. market at rock-bottom prices. It’s not just China, either. Countries like South Korea also dump product in the United States.
That’s unfair to American companies and workers like Patterson, who compete in an open market and play by the rules. And sadly, workers like Patterson are the ones paying the cost.
Patterson was a mill operator for much of his career at Allied Tube, and at one point worked as a cutoff operator. The workers bragged about being the fastest tube mill in the world, running tube at an astounding rate of 1,000 feet per minute. For the last two-and-a-half years at Allied Tube, Patterson was a crane operator.
But his career — and that of his coworkers — took a turn for the worse on Aug. 5, 2015, when plant executives informed workers that Allied Tube would close. Exactly two months later, Allied Tube permanently stopped production.
“It took my whole career to get there,” he said. “The crane operator was a good job and took me away from all the action. I thought I would retire from there, but the rug was pulled out from under me because of the steel dumped from China and South Korea.”
About 230 people lost their job when the plant closed; 176 people were members of the United Steelworkers (USW). Allied Tube was the oldest steelworker facility in the Philadelphia area, having been Steelworkers for more than 40 years.
As president of USW Local 404, Patterson felt it was incumbent on him to help his fellow steelworkers. Before the plant shutdown, Patterson organized a job fair and approximately 20 people got hired that same day.
But his real battle was yet to come.
“At the same time I was fighting feverishly with the company to complete the paperwork so we could apply for TAA benefits, which allow workers new job skill training and a small financial reimbursement,” Patterson recalled. “That was a struggle because these executives have all these multiple degrees but they don’t know anything. They were adamant about the reason they were getting out of sprinklers and fences is that they couldn’t compete in this market. I said, ‘if you were still making a million bucks a day off that product you wouldn’t be getting out of the market. So something is making you get out of that market.’”
Executives didn’t want to admit foreign imports were impacting their bottom line because they are a global company, Patterson believes. But it was important that pride didn’t get in the way — citing unfair trade was key to ensuring the government would provide TAA assistance.
“I needed them to understand that it is bigger than that,” Patterson said. “Once we got the paperwork done about three weeks ago, those men and women who were displaced that don’t have jobs will now have the opportunity to go to TAA meetings and hopefully individual schooling, additional income as well as some job placement opportunities.”
The hard work was worth it, Patterson said.
“I worked with those guys and girls for 25 years and I didn’t think it was right to just brush us off and by us not doing as much as we could,” he added. “Neighborhoods and communities are being devastated because the jobs are gone.”
But while many of the plants’ younger employees benefited from TAA, Patterson thinks TAA is really a folly for workers like him who are 55 and over.
“Our society has changed on a daily basis so talking about learning a different trade to do something where people are going to be looking to hire people, and now to compete with more young people and try to get one of those 18 jobs out of a group of 500 people,” he said. “It’s ridiculous at my age. For our government to say just go back and retrain, well that’s not realistic for everyone.”
For now, Patterson is on temporary assignment as a USW staff representative in the Philadelphia area. He is currently representing USW locals in contract negotiations at three smaller Pennsylvania steelmaking companies. His temporary assignment runs through June 12 but he has high hopes it will be extended.
“Since the layoff I’ve been doing some organizing with the union, with the international and now I’m working on some negotiating,” he said. “I’ve been fortunate.”