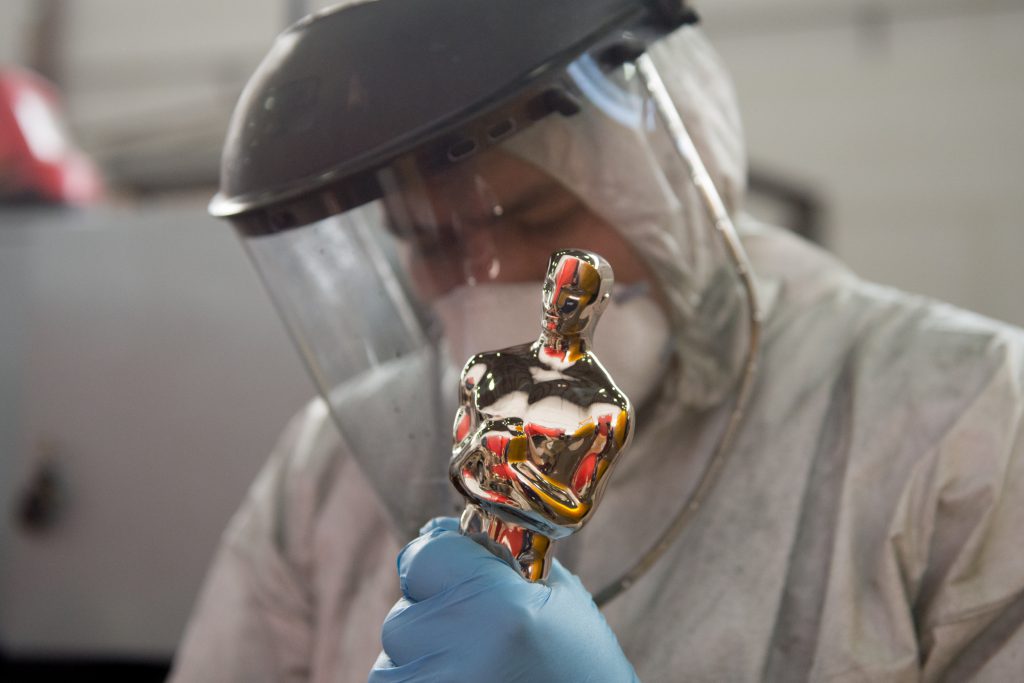
New York foundry Polich Tallix took over manufacturing the trophy in 2016.
Hollywood’s A-list will come together for the Academy Awards on Sunday night, with many of them hoping to head home with the film industry’s most-coveted prize — the Oscar.
From when the Oscar statuette was first conceived in 1927 by MGM art director Cedric Gibbons to Sunday’s ceremony, little has changed in the design of this coveted piece of hardware.
But there have been recent changes in its manufacturing.
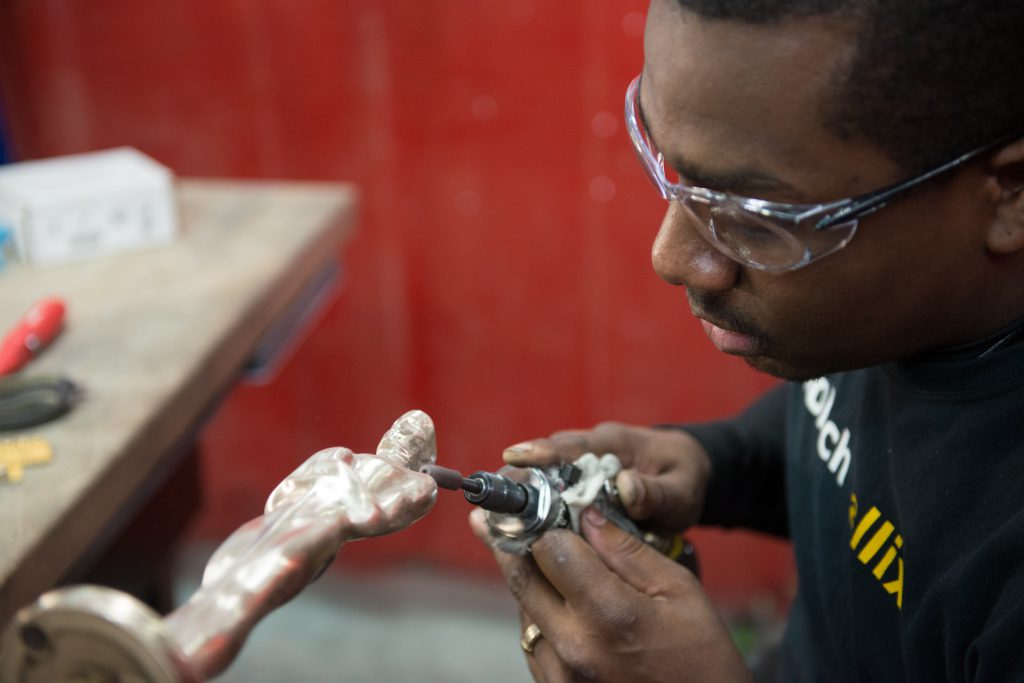
Polich Tallix, a fine arts foundry in Rock Tavern, N.Y., took over the manufacturing of the Oscar statuette in 2016 as members of the Academy sought to return to the roots of the original Oscar production process.
The original Oscar was sculpted in 1928 by Los Angeles artist George Stanley and was cast in bronze at the California Bronze Factory. This manufacturing process remained in place for many years, but during World War II, there was a shortage of metals and the Oscars were made of painted plaster.
Beginning in 1982, the Oscar statuette was manufactured in Chicago by R.S. Owens & Co. Instead of using bronze to create the bulk of the statue as was originally intended by Stanley, R.S. Owens produced the figures with a core of Britannia, a pewter-like alloy. They were then plated with pure gold.
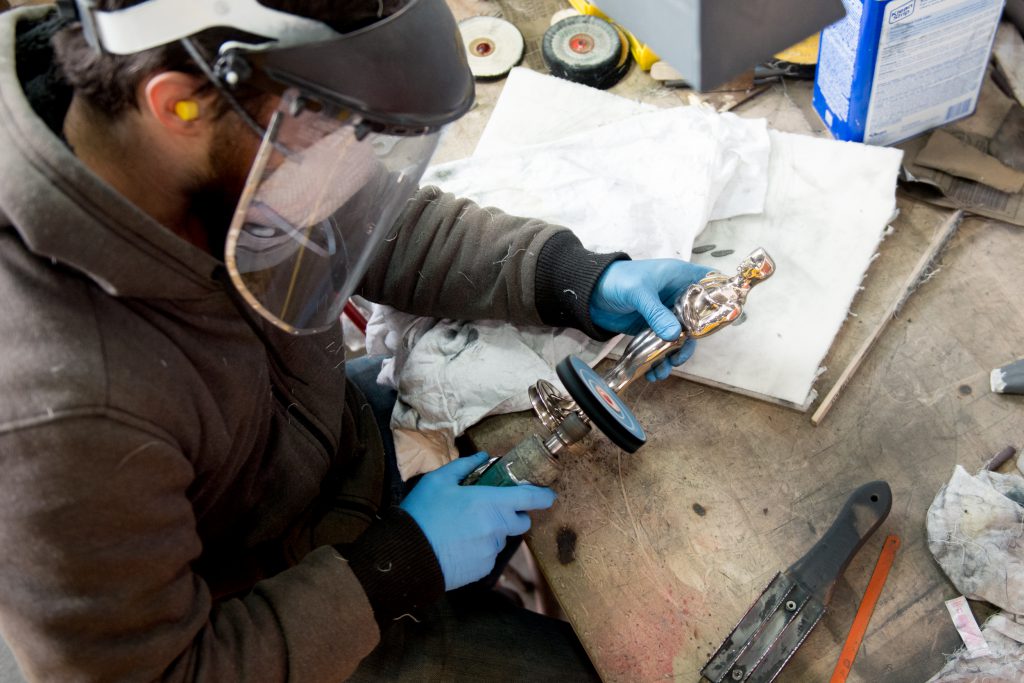
In 2016, the Academy wanted to return to the original design of a gold-plated, bronze statuette, but R.S. Owens did not possess the capabilities to melt and cast bronze.
That’s when Academy members came knocking on Polich Tallix’ golden door.
“The Academy approached us as an art foundry — which we are — that is capable of casting in bronze,” said Adam Demchak, vice president and general manager of Polich Tallix. “They brought us an original 1927 Oscar, and they brought us a modern Oscar, because there were features on each that they liked. We laser scanned them both and were able to marry the two together and they liked the design that had very little, subtle changes.”
While the Oscar is returning to its roots, a modern process helped with its new manufacturing process.
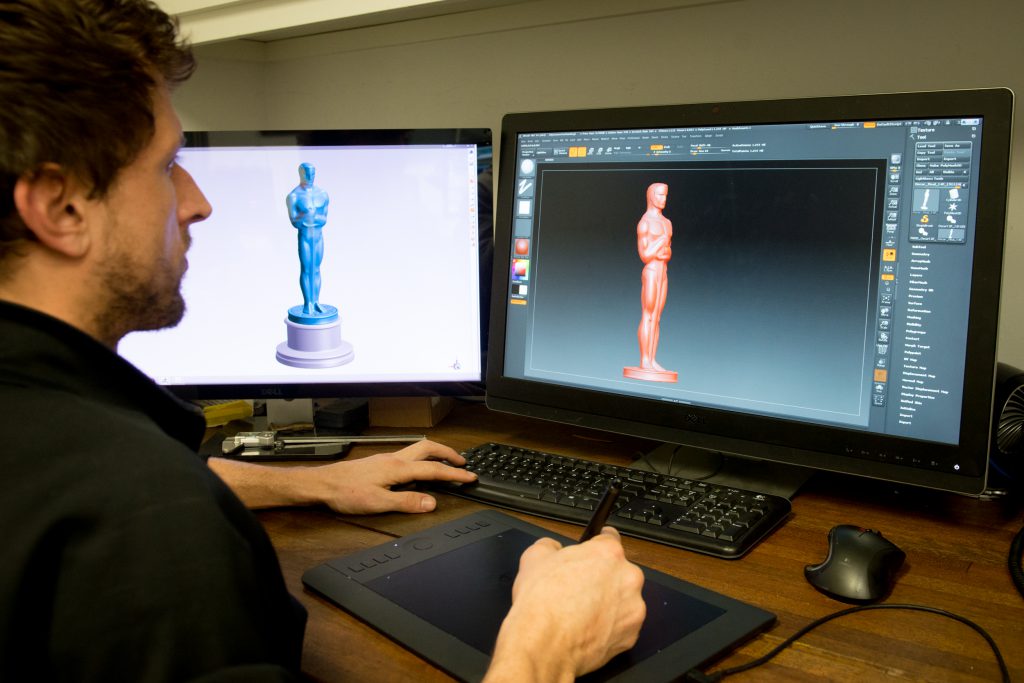
Polich Tallix designers created one Oscar statuette with a 3D printer, and then made a rubber mold from the finished 3D product. Wax outlines were made from the rubber mold and the more traditional process of creating a ceramic mold from the wax began. After the wax was melted out of the ceramic, liquid bonze was pour into the mold.
“We used sort of a modern process to get started and used that to feed the more classic, traditional process of casting,” Demchak said. “The bronze castings go into the finishing department and that’s where we have go back to the basics with hand sanding and polishing each individual Oscar.
“So you really go from a very contemporary technology in the investment casting to something that’s been around for decades. It’s an old school way of finishing metal with sandpaper and polishing pads used by hands. The bronze is always going to need to be polished.”
Polich Tallix also added a bronze base with a black patina that the statuette stands on. The base has added one pound to the weight of the statuette. The Oscar winner’s name will appear in polished bronze around this base.
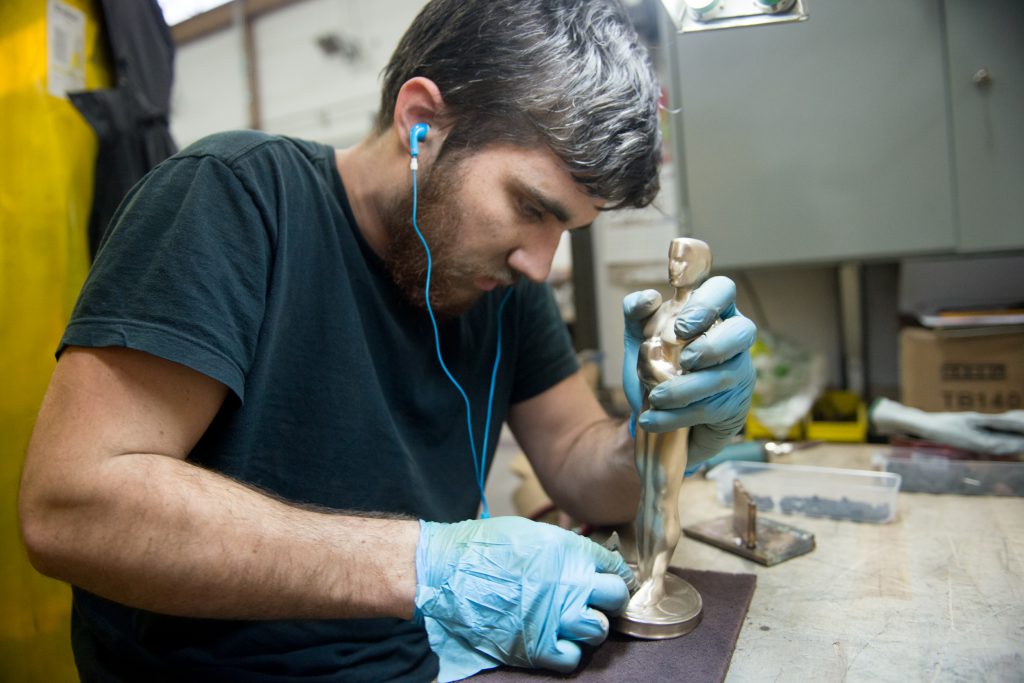
Every step of the manufacturing of the Oscar is done at Polich Tallix except for the gold plating. The statuettes are sent to Epner Technology in Brooklyn, N.Y., where they are plated in 24-karat laser gold that is significantly stronger than the pure gold that was used in previous years.
The Oscars are then returned to Polich Tallix, where engraving of the bronze bands that list every nominee in every category begins. Between the time the winner is announced and the recipient leaves the Dolby Theatre for a night of glamorous parties, the Oscar’s bronze base is affixed with a nameplate of the winner, category and year.
“We engrave a nameplate for every nominee. Otherwise we would know who won,” said Demchak.
Polich Tallix produced 60 Oscar statuettes for the 2017 awards. The company makes sure there are enough Oscar statuettes at the ceremony in case there are multiple winners in a certain category and to prepare for the rare possibility of a damaged statuette.
The completed Oscar statuette is 13 ½ inches tall and weighs 9 ½ pounds.
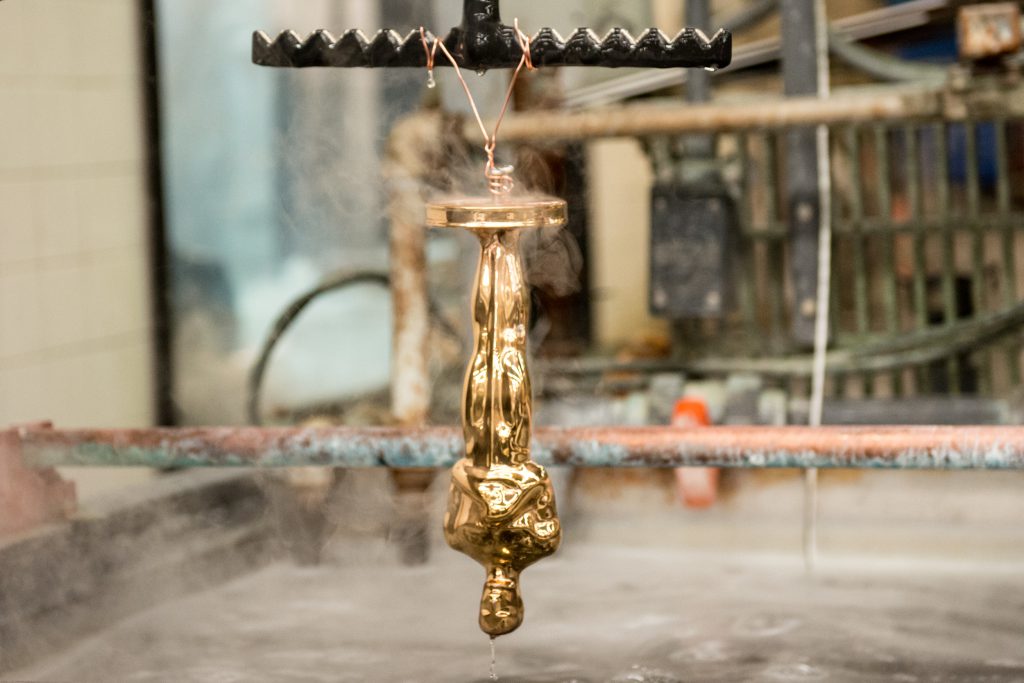
Polich Tallix has been in business for 47 years. Founder Dick Polich, now 85, opened his metal-casting company in an area of New York inundated with sculptures and other artists.
Rock Tavern is about an hour and half from New York City in the Hudson Valley near Newburgh. Polich is still active in the company, but he hired 35-year-old Demchak to take care of the day-to-day operations.
Polich Tallix is one of the largest art foundries in the country, with 83 full-time employees and a manufacturing facility that is just less than 100,000 square-feet.
‘For the most part, we work with art,” Demchak said. “We cast and fabricate metal sculpture and that’s probably 95 percent of our business. We do a little architectural work but mostly we work for artists and galleries.
“If you know the sculpture world, you can basically pick a sculptor and we probably worked for them. We have projects going on right now for Jeff Koons, Ursula von Rydingsvard and Joel Shapiro. We keep busy. Right now I can tell you we have 114 projects going. These vary from small sculpture repairs to large, year-long production projects. So we run the gamut. Nothing is too big and nothing is too small.”
Hollywood filmmaking is an American industry, and its most prestigious award is Made in America.
Visit the Polich Tallix website.