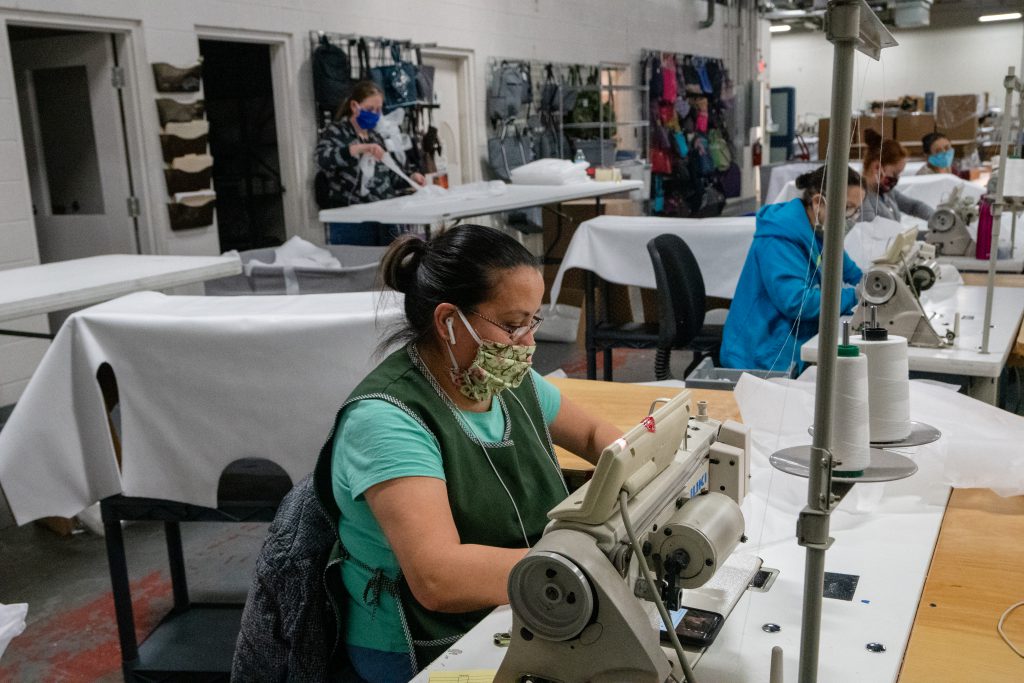
The Indiana company is donating a mask to an essential worker for every mask sold.
Interior designer Cinda Boomershine first garnered national recognition in 2003 when she became a member of the cast of the TBS television show Movie and a Makeover.
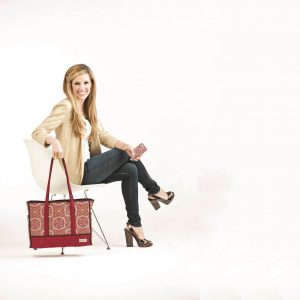
She parlayed the success of her 9-year tenure on the show into a successful Made in America handbag and tote business, cinda b.
While her run on Movie and a Makeover ended in 2011, it would not be the end of makeovers for cinda b.
The handbag company is now churning out protective face masks at its manufacturing facility in Fort Wayne, Ind., donating a face mask to an essential worker for every one sold to the general public. The facility is also making hospital isolation gowns, face shields and even portable beds for the military.
“We are doing facemasks in cinda b patterns,” Boomershine said. “Our current fabric that we use to manufacture the bags are printed on polyester, so we are now printing the patterns on cotton, which is better for a mask. We are printing the pattern in America, and we are manufacturing the masks in America.”
Although the company still bears her name, Boomershine sold her ownership of cinda b in 2015 to her manufacturing partners, Bob Hinty and Adlai Kunst, in order to spend more time with her young children. Hinty owns Hentz Manufacturing, the facility in Ft. Wayne where sewers produce the cinda b bags, and Kunst oversees his Fabri-Quilt fabric printing company in Kansas City. Boomershine remains involved as creative director with a vested interest in the company.
Everyone is aligned when it comes to making personal protective equipment (PPE) like face masks, an effort that began about two months ago.
“My doctor approached me and said they were really running low on these things and this looks like it could get bad,” Hinty said. “I made him some isolation gowns at first, because he said that’s what they would be running lowest on at first. Less than a week after, I got a call from the local hospitals asking if we could make gowns and masks for them.
“And it’s not just hospitals. It’s nursing homes and doctor’s offices. The state of Indiana is buying our PPE and distributing it to the Indiana hospitals.
“We are selling everything. I had a request from a hospital up in the New York/New Jersey area for 4 million patient gowns, but we are not making patient items right now. We only make things that would be used by the front-line people, primarily face masks and isolation gowns.”
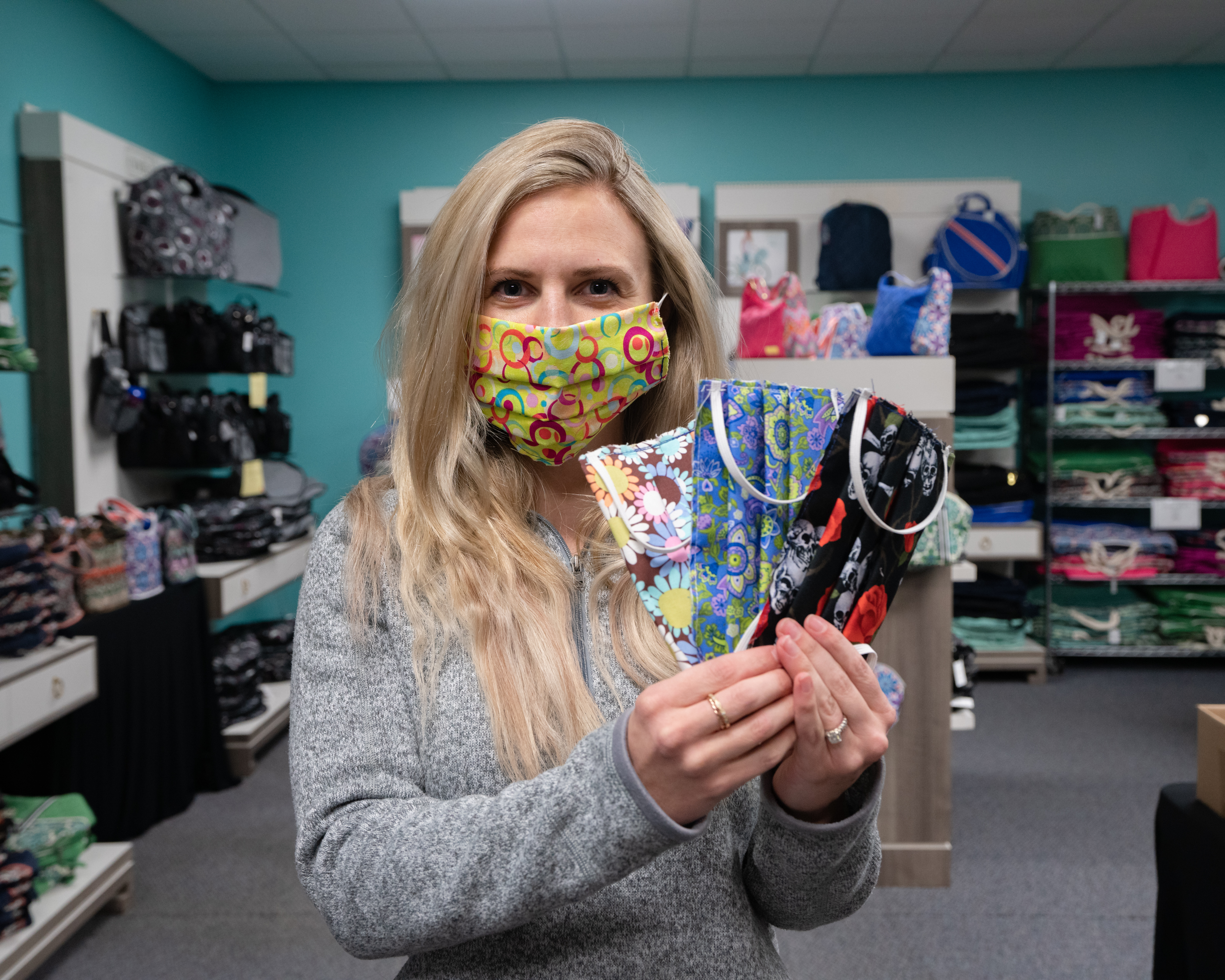
Boomershine said she first realized the need to make face masks during a trip she took with her husband and two children to Costa Rica back in February.
“There were rumblings of the virus, but nobody was really talking about it at that time,” Boomershine recalled. “My kids touch everything, so I whipped up a couple of kids’ face masks for the plane trip and I posted it on Instagram. This was three weeks before everything shut down, but I got an insane response, so I called Bob. The wheels started turning and once it hit a critical point Bob realized there was a definite need and he switched the factory over. They did it in a matter of days. It was amazing.
“We had a couple of conversations about it, and all of a sudden Bob just jumped in, and it was early. Bob’s primary focus has been getting it to the hospitals but after the Instagram post, everybody wanted face masks.
“March was all just hospitals. In April, we offered masks on the cinda b website, and now we have printed fabric in our patterns and are making masks in cinda b patterns.”
The face shields being manufactured by Hinty’s team of 70 employees are made from plastic on that is normally used for making the cinda b hanging organizer. It is a 20-gauge plastic, and Hinty decided to coat the plastic with a product called Frog Spit, typically used by scuba divers and snorkelers, that prevents the shields from fogging.
“I just went out to the local dive shop and they had a bunch of products there, and I asked which one is the best and they said Frog Spit,” Hinty said. “We try to source all products from the United States.”
Hinty has plenty of fabric in stock now that he has slowed production on cinda b bags and most of the other products he manufactures. With the help of his partner Kunst in Kansas City, he can secure plenty of fabric for face masks and gowns. Kunst is currently printing several cinda b patterns for the next batch of face masks.
“When I started making PPE, my goal was to make 100,000 of each product: face masks, face shields and isolation gowns,” Hinty said. “We switch up production and change the mix depending on what the requests are from the customers. Because we have the materials in stock and are manufacturing right here in Indiana, we are able to change the mix on any given day. We will likely make more than 100,000 of each item, as there probably will be a continuing need for face masks and gowns.”
Before PPE production began, Hinty also had to change the makeup of his 35,000 square-foot manufacturing plant so that workers could maintain social distancing and be protected with the same gear they were making.
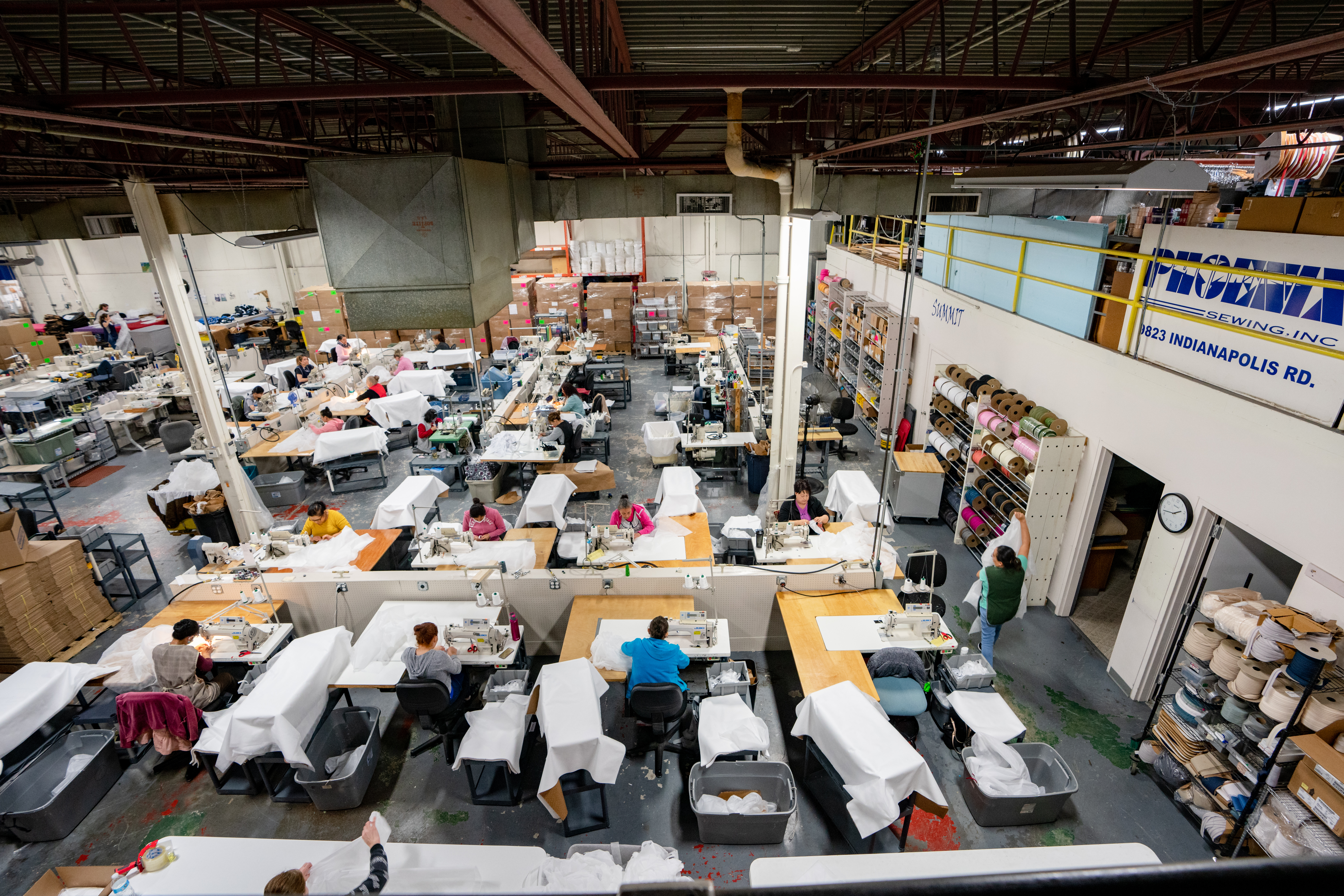
“We do keep people six feet apart, and the way it is set up people are kind of staggered to keep them apart,” Hinty said. “We have multiple lunch hours and we have people doing full-time cleaning now to keep the place constantly wiped down. Everybody is wearing masks. If you go into the factory, you have to wear a mask.”
The Hentz Manufacturing workforce is glad to be back working and contributing to the battle against COVID-19. Hinty has ramped up production to approximately 15 lines of product and plans on hiring another 30 people as soon as possible.
Hintz, a native of Chillicothe, Ohio, built and opened his Ft. Wayne factory in 1994. At the age of 65, he is happy he has the flexibility of being a domestic manufacturer.
“I am 65 years old, but really 130 in manufacturing years, because it is a lot more demanding than sales or marketing because the devil is always in the details,” Hintz said. “But being an American-made company is another advantage because if somebody changes their minds or tastes change, we can quickly pivot. Cinda b masks were not available three months ago, but now they are.”
Although the company is making PPE, it continues to sell its Made in America bags and accessories. Hinty’s strategy for the cinda b brand entailed more of a direct-to-consumer online product, which is paying off now that most retail outlets are closed.
But Boomershine spent years cultivating her retail partners and is concerned about their future.
“I worry about the retailers surviving after this virus,” Boomershine said. “The good ones, the more sophisticated ones will make it, but there is going to be a lot that don’t.
“I worked with those retailers for years, so we worked really hard to protect them. It is a tricky walk to walk to have retailers selling your products and to be selling direct to consumer. You want these people to be cinda b retailers, and you want them to be in their town supporting and spreading the word and all of that. But at the same time the world is changing. Everybody is ordering online more and more, and you cannot ignore that fact.”
Boomershine is proud that her bags and totes remain an American-made product and Hinty shares that sentiment. He cites the Berry Amendment, passed by Congress in 1941, that requires the Department of Defense to give preference in procurement to domestically produced, manufactured or home-grown products, including food, clothing, fabrics and special metals.
To put it simply, when the U.S. government is buying essential military goods for the benefit of Americans, those goods must be Made in the U.S.A.
“A lot of companies that are importing stuff are still waiting for orders they have placed overseas,” Hinty said. “I would like to see us follow the Berry Amendment, not just to military stuff, but a certain amount of medical stuff that we should make in this country at all times. The Berry Amendment’s products only applies to military, but it should apply to anything our government buys, in my opinion. I think now is a good time to get people to take a look at that and understand what that means.
“We should never put ourselves in this kind of position ever again. It is a product that we are in desperate need for as a country. I’m dedicated to making product in America. I have no interest in making product overseas. There is plenty of market here.”
Editor's Note: Blogs like this one are intended to highlight companies that support American jobs and that make great products in the United States. We rely on companies we feature to provide accurate information regarding their domestic operations and their products. Each company is individually responsible for labeling and advertising their products according to applicable standards, such as the Federal Trade Commission's "Made in USA" standard or California's "Made in USA" labeling law. We do not review individual products for compliance or claim that company products comply with specific labeling or advertising standards. Our focus is on supporting companies that create American jobs.